Work Package 3:
WP3: Automated and robotic sample delivery for high-throughput experiments
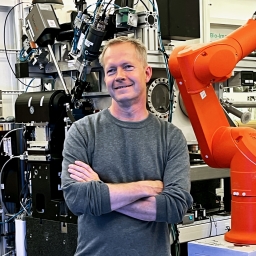
Q&A with Dr. Alke Meents, HIR3X WP lead on “Automated and robotic sample delivery for high-throughput experiments”
What are the current challenges in making X-ray Free Electron Lasers (XFELs) more reliable?
A special features of XFELs are their high intensity X-ray pulses coming at high repetition rate. For example the LCLS at the SLAC National Accelerator Laboratory can generate high power X-ray pulses at 120 Hz, while the European XFEL can even generate repetition rates up to the megahertz for a short time.
Generating these intense pulses, we of course want to use all of them to their full potential to get the highest resolution information possible from our samples in short time. But for many applications, including my own work in crystallography, the samples are usually destroyed, which means you need to replenish the samples at the same rate as the pulses arrive.
This means that at LCLS every 8-10 milliseconds you need a new sample, and if you go to the megahertz, this means every microsecond, meaning in principle you need a million samples each second. That’s not always possible.
That’s where the main challenge lies – how to create a sample delivery technique that makes efficient use of the limited beam time to get the best information from a limited supply of samples.
What sample delivery techniques have you tried?
Historically, there’s been a few different sample delivery techniques. In crystallography, the most common method is to use liquid jets, where the sample is suspended in a liquid and then pressed through a nozzle at extremely high speeds, where the X-ray pulses then hits one of the crystals by chance, i.e. it has a low ‘hit rate.’ Other methods use variations on this, for example increasing the viscosity of the liquid to increase the chances of the X-ray pulses hitting the sample, though these measurements usually come with higher X-ray scattering from the viscous matrix material which creates more background noise. Crystals can also gather at the exit of nozzle, and this makes clogged nozzles a common issue.
My favourite approach is what I’ve been working on for the past decade – the ‘fixed target delivery’ system. With this method the samples are immobilized on a very thin substrate just a few microns thick. We preferably use silicon membranes for this, which only produce very small background scattering. Ideally you can even have a substrate which is ‘micro-structured’ consisting of a periodic array of micropores, which means your sample crystals arrange themselves according to the substrate’s pattern. This lets researchers systematically scan them through the beam and achieving very high ‘hit rates’.
We started researching and using this system back in 2015, and after a decade of work we’re now seeing a steep increase in requests from researchers to analyse their samples using this method.
This fixed substrate method has the advantage of having little-to-no background noise and having predefined positions on the substrate means that you have a reliably high hit rate. For example one recent experiment we did at LCLS had hit rates of 60-70%, which means really efficient measurement times for researchers. To put that in perspective, using a viscous jets analysis might get hit rates of only 5 – 10 %.
Is there any disadvantage?
Nothing’s perfect – what makes it challenging is to synchronise moving to different substrates with the X-ray pulses. We both have to move it to the next pore in the substrate, which is usually only 50 microns away, while also making sure you’re at the at the position where you expect the next crystal to be when the next X-ray pulse comes.
How else do you reduce signal noise, for example when the X-rays pulses are moving though air?
Air is not good. It causes significant scattering of X-ray pulses. Ideally the sample would be in a vacuum environment to reduce this background noise, but this would substantially complicate sample delivery.
Instead we have developed a device where the X-ray beam is travelling while enclosed in thin capillaries made of tantalum. These capillaries absorb all the scattered radiation caused by air so it doesn’t reach the detector. These capillaries are placed as close as possible in front of the sample, and then just a few millimetres after the sample so that it can guide the direct undiffracted beam through a hole in the detector while all the air-scattered X-rays are absorbed by the capillaries and consequently do not contribute as noise to the detector image.
In total, the beam only passes through 5-6 millimetres of open space. Even in this small amount of space there are ways to reduce scattering. We ‘flush’ this space with helium, which is a lighter atom and so has less electrons that could scatter the beam. This means we get as close as possible to a vacuum environment for the beam without needing a complicated vacuum chamber.
You also mentioned you have worked on improving the targeting of the radiation pulses so that it does hit every target in the silicon membrane. How are you doing that?
We usually use thin membranes from silicon for synchrotrons. Silicon is crystalline, which means that when the X-rays hits it, they are scattered into well-defined directions. These can then be easily excluded from the data analysis. The problem with silicon is that these scattered X-rays from a single pulse could accidentally hit the detector so strongly that the beams destroy it.
In HIR3X we decided to move to Kapton foil as an alternative membrane material. These foils can extremely thin, in the project to developed chips that are only 3 microns thick. This helped us avoid the potential detector damage issue of the silicon membrane while still providing very low background scattering levels.
Another aspect of your work in HIR3X was developing automation solutions for sample delivery. What work did you do?
One of my major goals has been to make measurement techniques more efficient and automated. At DESY we’ve been developing sample-changing robots for synchrotrons for the past decade, most notably publishing a paper in Science about how we achieved measurements of more than 6000 crystals in less than 4 weeks.
In the HIR3X project we used that experience push this further. For example, we developed a robot specifically for the fixed target sample holders we developed. Once the target has been placed on these chips, they can then be placed in a storage ‘hotel’ at the beamline. The robot can then take each chip from the hotel and place it automatically on the goniometer (where the sample is rotated and exposed to the X-ray pulses).
Usually this is a manual intervention, which you want to avoid, because people are too slow to change the chips. It usually takes about 5-10 minutes to enter the hutch, change the chips, and re-activate the radiation interlock. Developing a robot to exchange the chips means this we can get this changeover time to around one minute. This might sound like saving just a small amount of time, but it means that the users don't need to be physically on site anymore. Using the robots you can run for beam for up to 10 hours without entering the hutch. Since the robots are controlled remotely, we can in principle do this from any place in the world. We have already set this up at the PETRA-III synchrotron source at DESY and we will soon try it at the European XFEL and potentially also at LCLS.
It must be satisfying to see your team’s hard work pay off.
Even though my scientific focus is in protein crystallography and structure based drug discovery, I often describe my work generally as engineering. I find it just as interesting to view research questions on how proteins interact with ligands through an engineering lens! Whereas the design of our hardware for the diffraction experiments happens on the millimeter to centimeter scale, the design of new ligands and inhibitors takes place with similar principles on the Angstroem range – 6 -7 orders of magnitude smaller.
I’m happy that we could use our new substrate holder designs and collaborative robots to help HIR3X reach its goal to make research more efficient at synchrotrons. I think if you work with robots a more daily basis, it’s not so exciting, but the novelty is that collaborative robots can sense collisions and then stop immediately, allowing that people and robots can work safely together.